Die Mittermühle dürfte, wie der Name schon sagt, einmal als die Vierte in der Mitte aller Mühlen am Mühlbach gelegen sein.
Im Jahr 1802 gehörte die Mühle dem Mathias Treiber. Zur Mühle gehörte auch eine Säge, die mit einem Blatt betrieben wurde. Die Säge wurde 1958 stillgelegt.
Seit 1836 ist die Mühle im Besitz der Familie Engelsberger, die auch Erbhofbauern des An-wesens sind. Auf dem Bild sind die Großmut-ter, die Eltern und Schwestern des heutigen Besitzers vor der Mühle zu sehen.
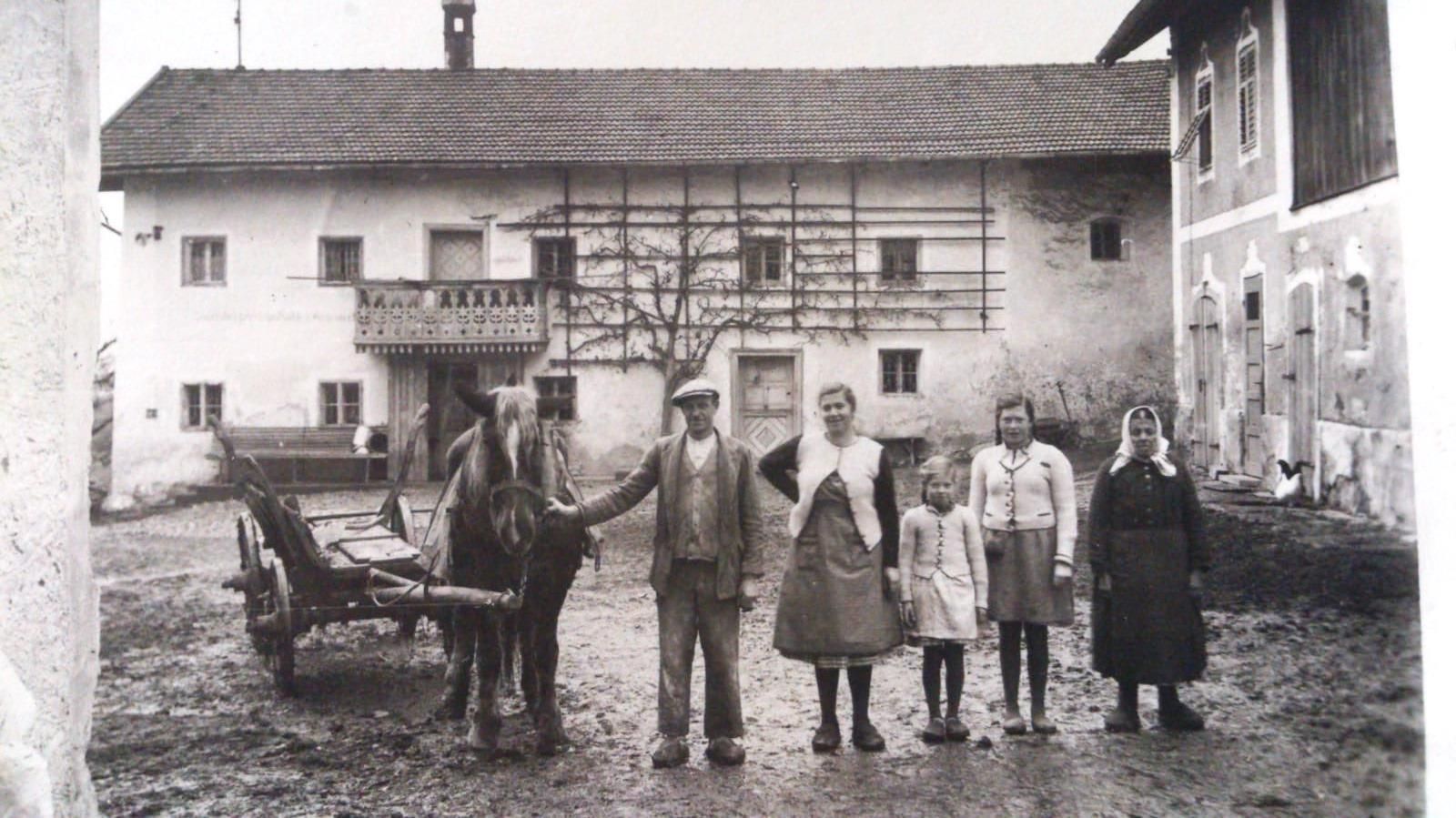
„Die neue Mühle, so wie sie auf den Fotos zu sehen ist, hat mein Vater 1953-1954 umgebaut. Die alte Mühle wurde völlig abmontiert. Das Haus und die Mühle wurden dann aufgestockt und neu eingerichtet. Betrieben wurde die Mühle bis 1981“, erzählt Josef Engelsberger, der letzte Müller der Mittermühle und erklärt noch immer begeistert von seiner Arbeit anhand einiger Fotos den Ablauf bei der Mehlherstellung:
„Bevor das Getreide gemahlen wird, muss es verschiedene Reinigungseinrichtungen durchlaufen. Die erste Reinigung übernimmt hierbei der Aspirateur (franz. Vakuum). In ihm werden die Trennung von Stoffen nach unterschiedlichem Gewicht in einem Luftstrom und die Trennung nach unterschiedlicher Größe durch schwingende Siebe bewerkstelligt. Mit einem groben Sieb werden größere Teilchen wie Erbsen, Mais und Steinchen aussortieren und durch das feinere Sieb Teilchen wie Sand, Bruchkorn, oder kleine Samen.
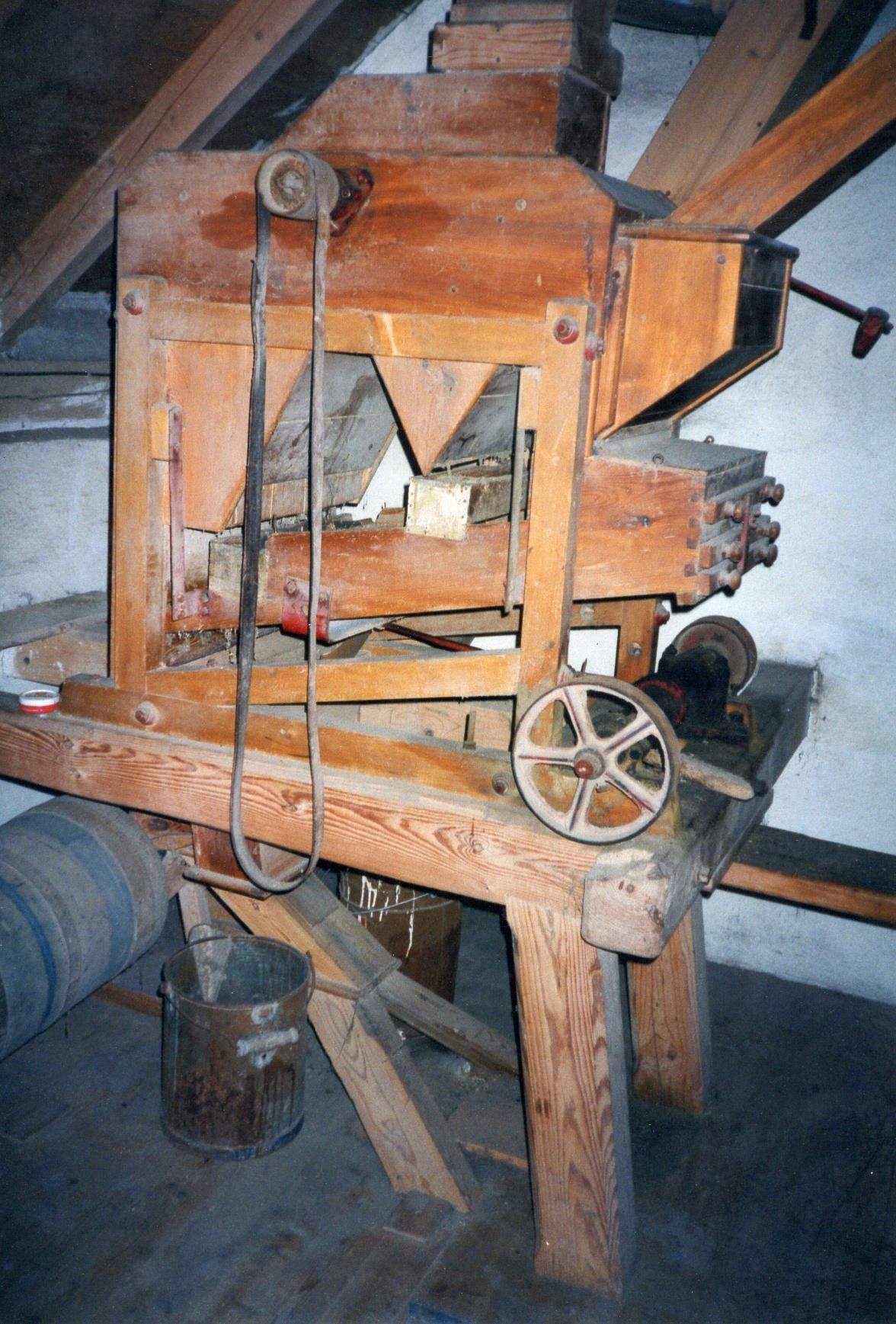
Im Trieur (franz. auslesen) werden dann eine Reihe von Wildkrautsamen, wie z.B. Raden und Wicken, die etwa die gleiche Größe haben wie das Korn, sich aber in der Form unter-scheiden, aussortiert.
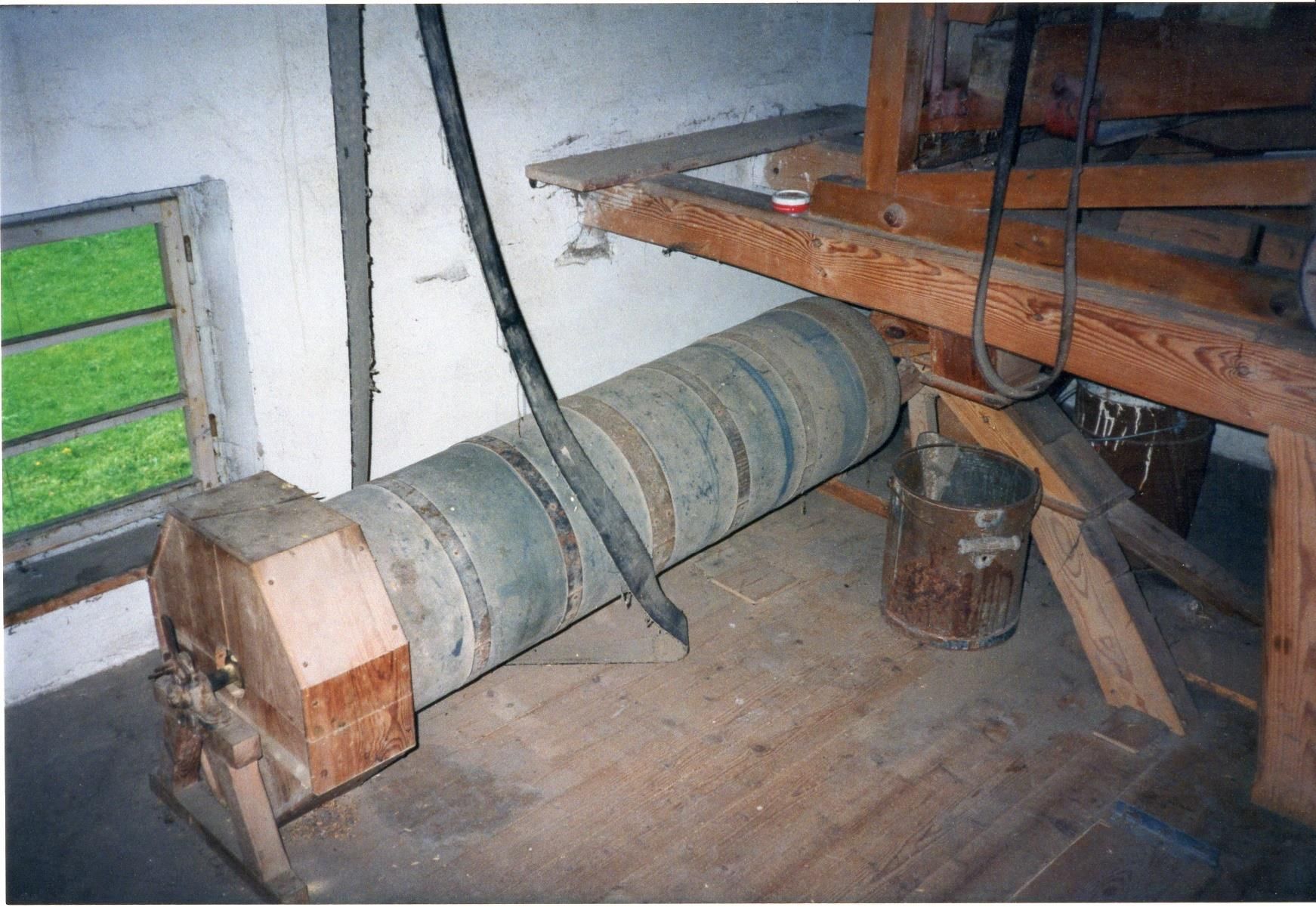
Es folgt die Schälmaschine, in der die harte, holzigen Schale zum Schutz des Keims und des Mehlkerns entfernt wird. Ein Schlägerwerk wirft dabei das Getreide gegen einen Schmirgelmantel innerhalb der Maschine.
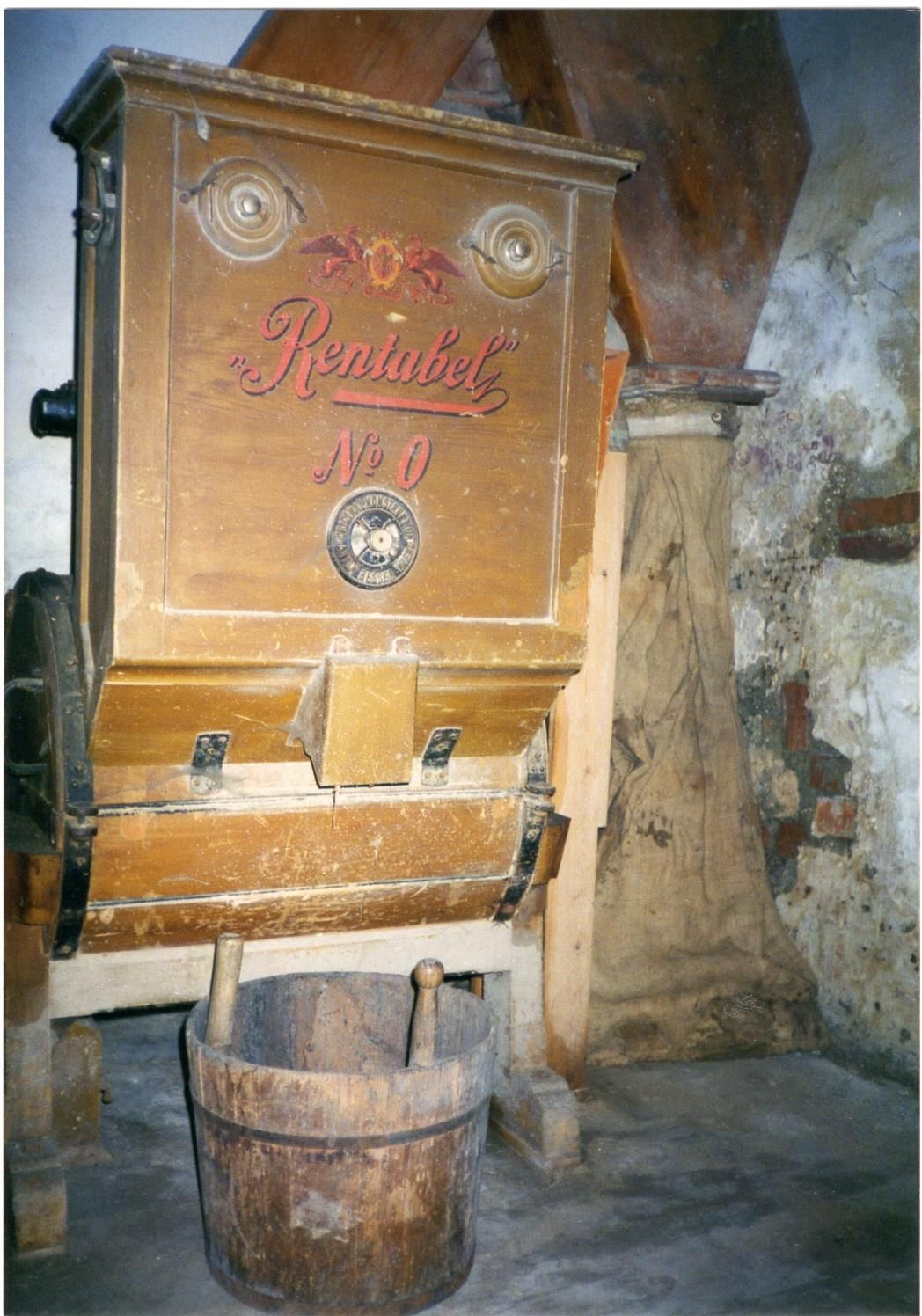
Nach dem Schälen werden Verunreinigungen, wie angerissene Teilchen der Schale, des Keimlings und eine bedeutende Menge Staub in der Bürstmaschine beseitigt.
Die Walzenstühle übernehmen die Vermahlung des Korns. In zwei geriffelten Hartgusswalzen, die sich mit unterschiedlichen Umfangsgeschwindigkeiten drehen, werden durch den Druck der Riffeln die Teilchen zerschnitten und infolge der Voreilung der einen Walze auseinandergerissen.
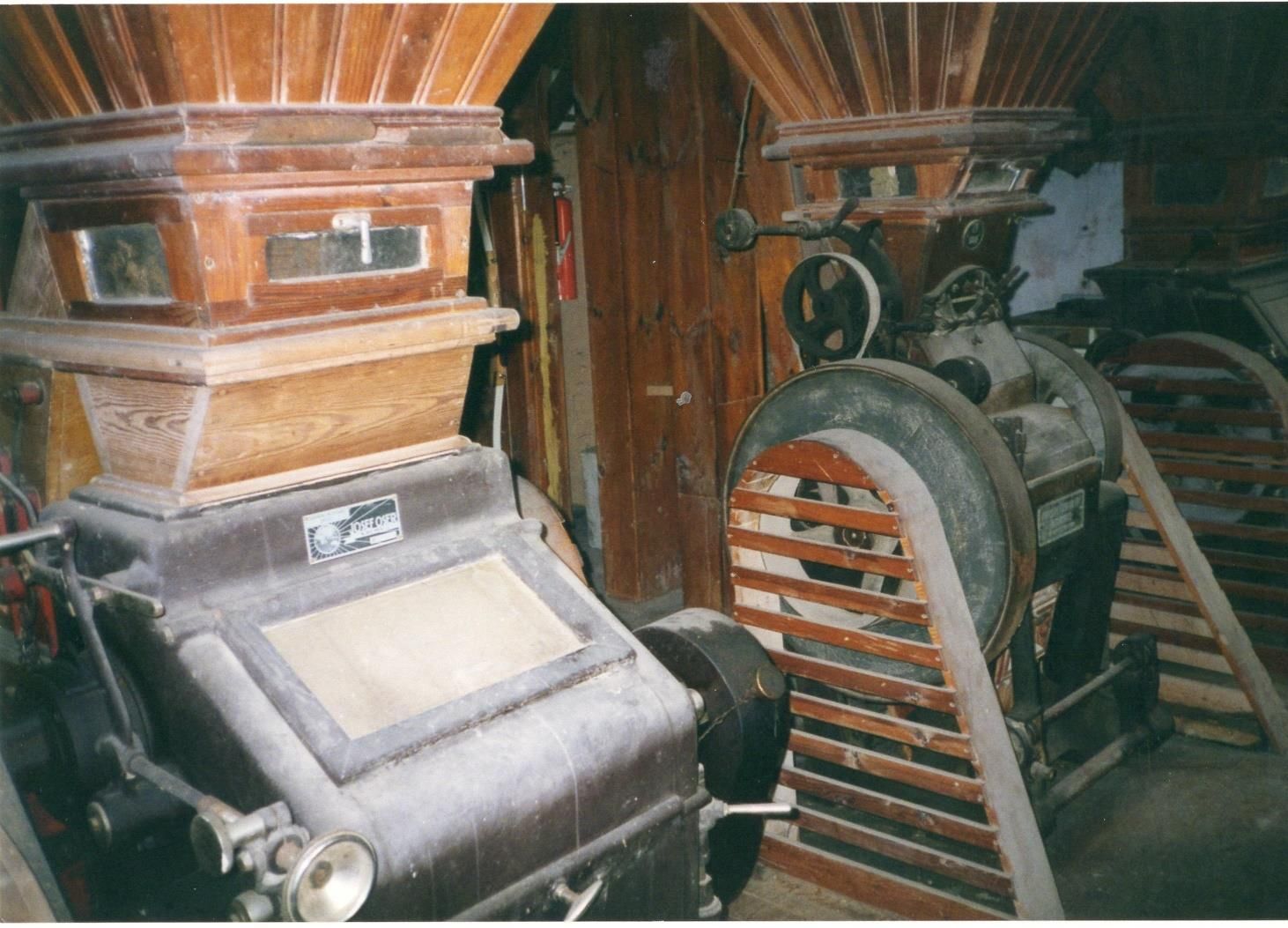
Um das Gemisch aus Mehl, Dunst, Grieß und Schrot der Walzenstühle voneinander zu tren-nen, bedient man sich des Plansichters. Dieser besteht aus Siebstapeln mit jeweils 12 Siebkästen. Ein Kurbeltrieb versetzt ihn in kreisen-de Bewegung und erzeugt eine Schichtung des Mahlgutes auf dem Sieb, d.h. schwere Teile wie Mehl und Dunst sinken nach unten und kommen unmittelbar mit der Bespannung in Berührung, während die leichteren Schalenteilchen oben „schwimmen“. Dadurch lassen sich die Mehle sauber absichten.
Die Kombination aus Walzenstuhl und Plansichter wird „Passage“ genannt, von denen eine moderne Mehlmühle eine Vielzahl aufweist. 14 Passagen und mehr sind gängige Größen.
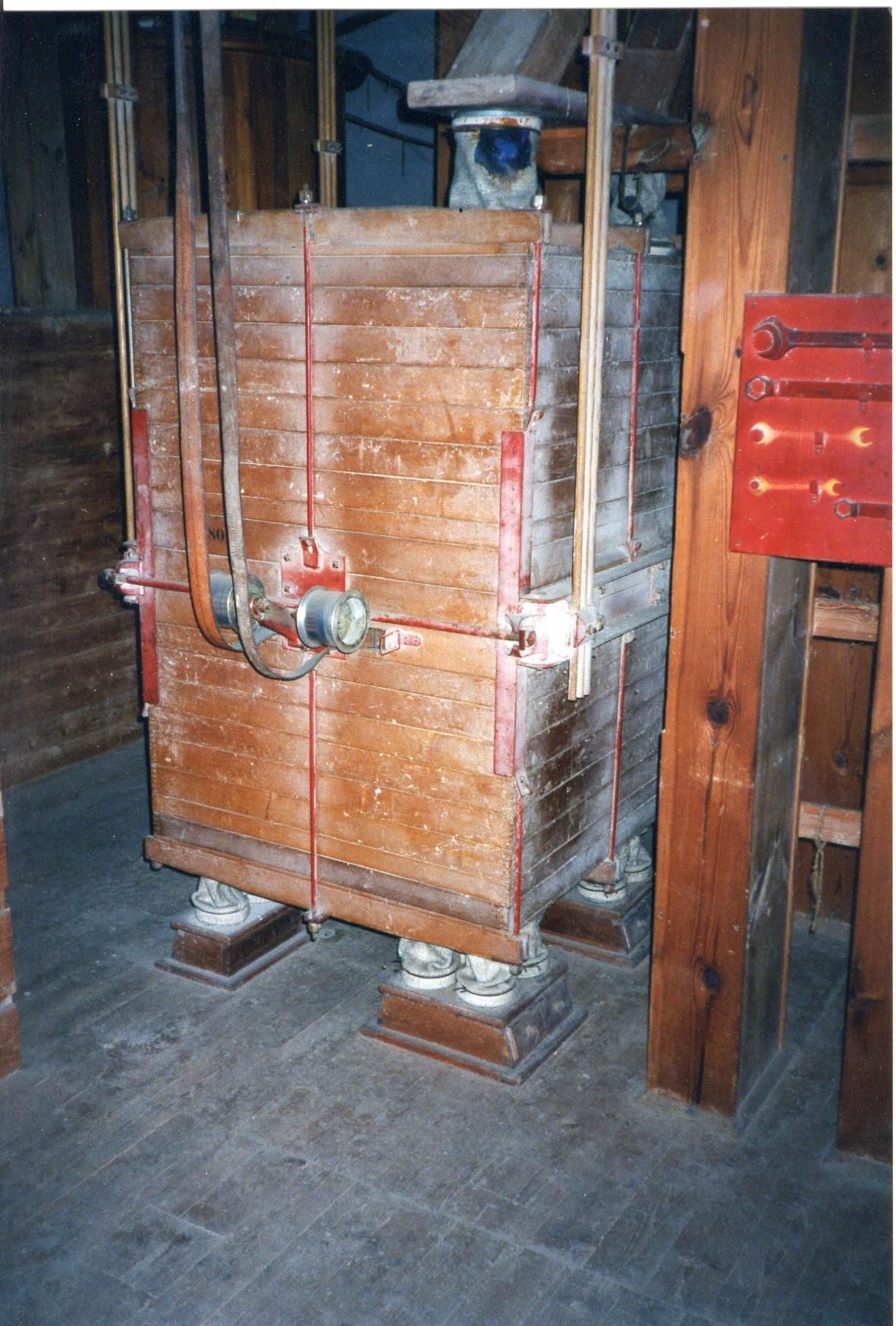
Das Getreidekorn wird nicht mit einem Male zu Mehl vermahlen, sondern in mehreren Stufen. Infolgedessen entsteht während des Mahlprozesses Mehl unterschiedlicher Qualität und Zusammensetzung.
Der Müllermeister stellt nun die gewünschte Mehlmischung sackweise zusammen. Diese schüttet er in die Mehlmischmaschine, in der eine Kegelschnecke läuft, die oben einen größeren Durchmesser hat als unten und so für eine gute Durchmischung sorgt.
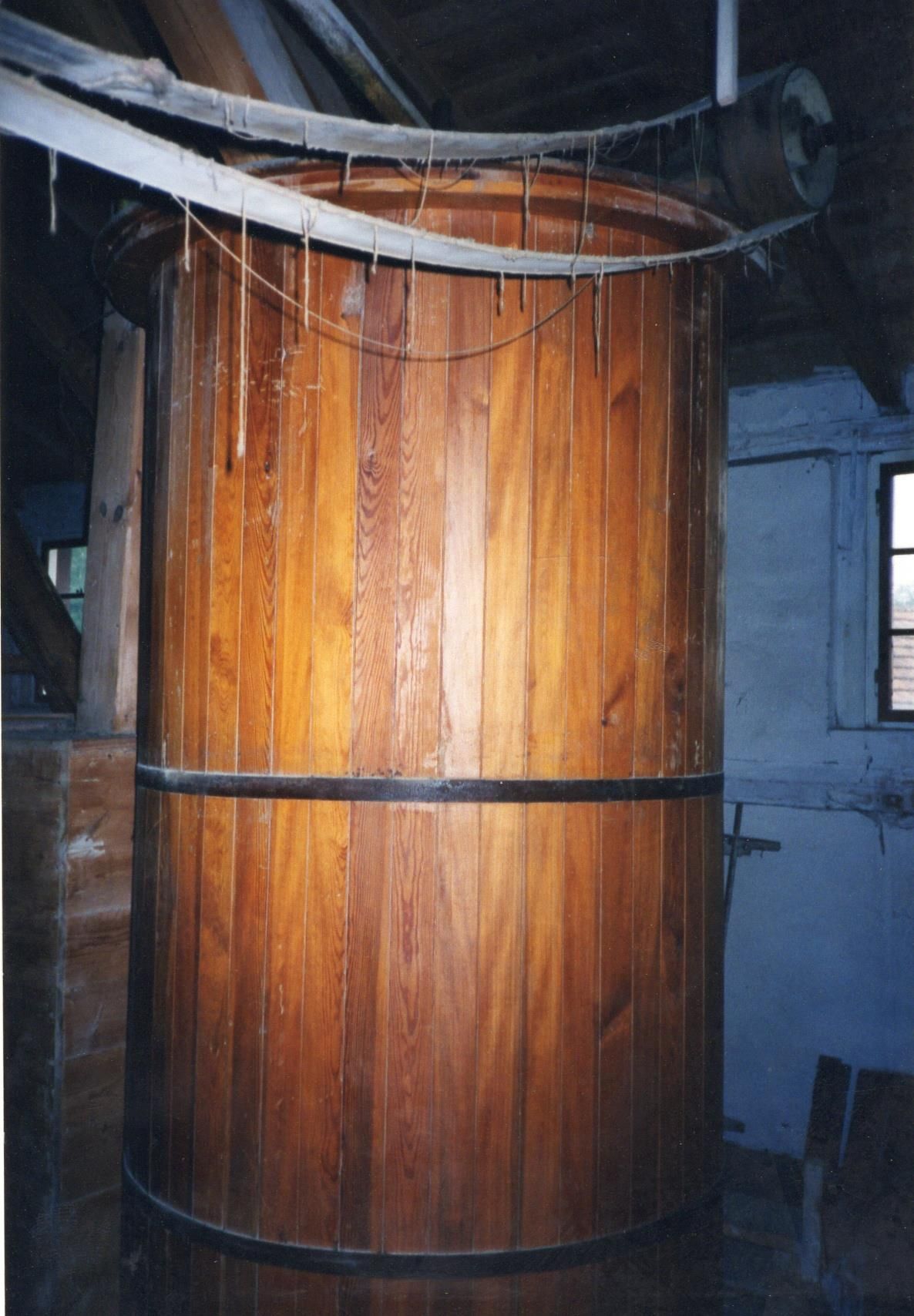
Vom Wasserrad bis in den letzten Winkel der Mühle erstreckt sich ein ausgeklügeltes System von Antrieben und Gurten.
Der Hauptantrieb führte die Wasserkraft bis zur Decke des Mühlendachs. Mit Riemengetrieben, sogenannten Transmissionen, wurde die Kraft auf die Maschinen verteilt. Ja sogar Aufzüge (Elevatoren) konnten Mehlsäcke befördert werden.“
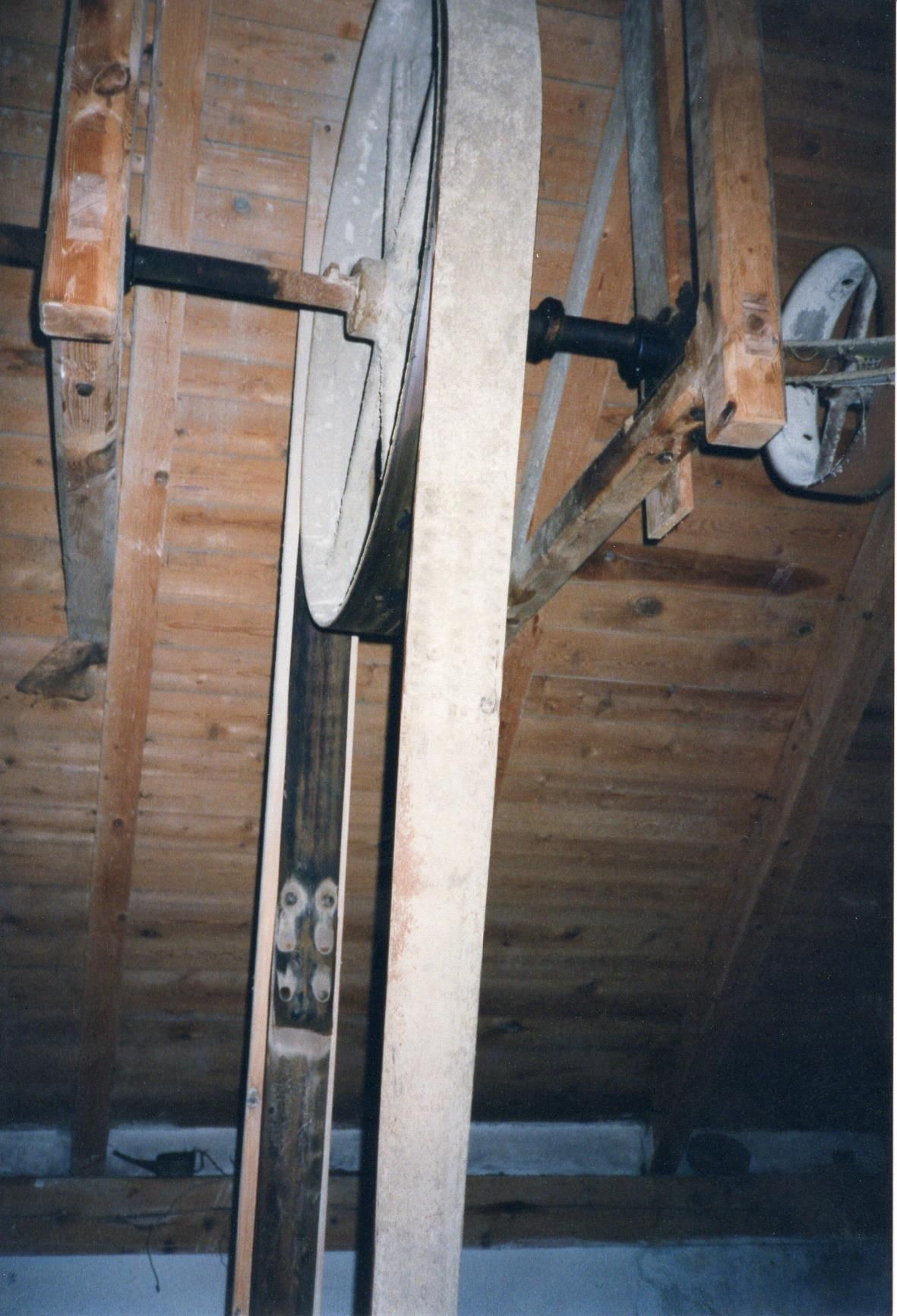
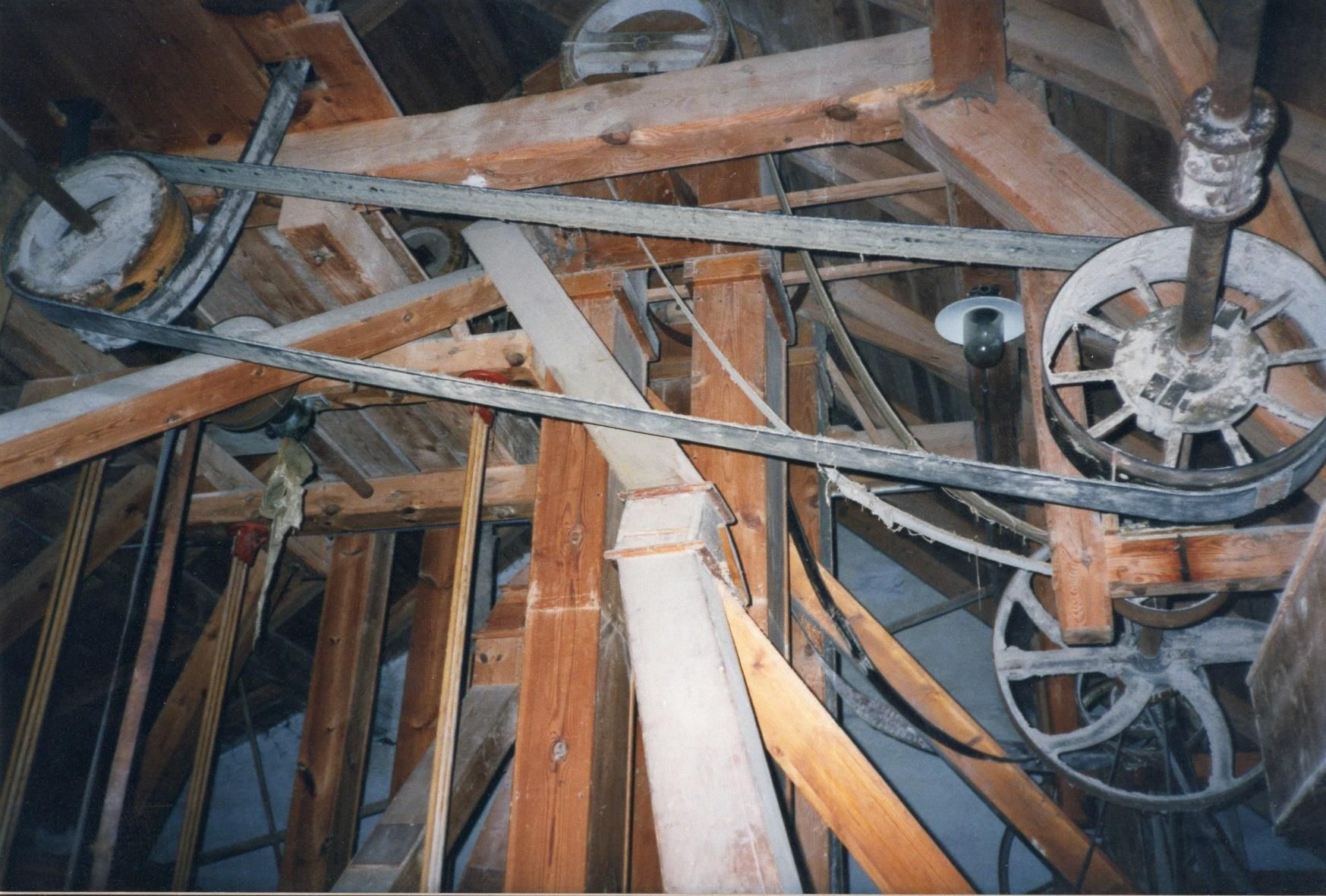
Interessant auch die Bezeichnung der „Type“ des Mehls. Die Type W480 z.B. gibt den Mineralstoffgehalt von 480 mg je 100 g Trockenmasse an. Der Mineralstoffgehalt (= Aschegehalt) wird beim Verbrennen einer gewissen Menge Mehl bei 900 °C bestimmt.
Weiter zur Kagermühle
Zurück zu Die Mühlen von Ostermiething